The great explorer of the truth, the master-builder of human happiness no one rejects dislikes avoids pleasure itself because it is pleasure but because know who do not those how to pursue pleasures rationally encounter consequences that are extremely painful desires to obtain.
Read MoreIntroduction
Steel manufacturing is a critical industrial development pillar, supporting the construction, automotive, and infrastructure sectors. Despite its importance, the steel industry is challenged by high energy demands, environmental impacts, and a pressing need for consistent quality control. Large-scale operations often lead to substantial inefficiencies and increased production costs. Addressing these challenges effectively is essential for maintaining a competitive edge and ensuring sustainable
practices in a globally interconnected market.
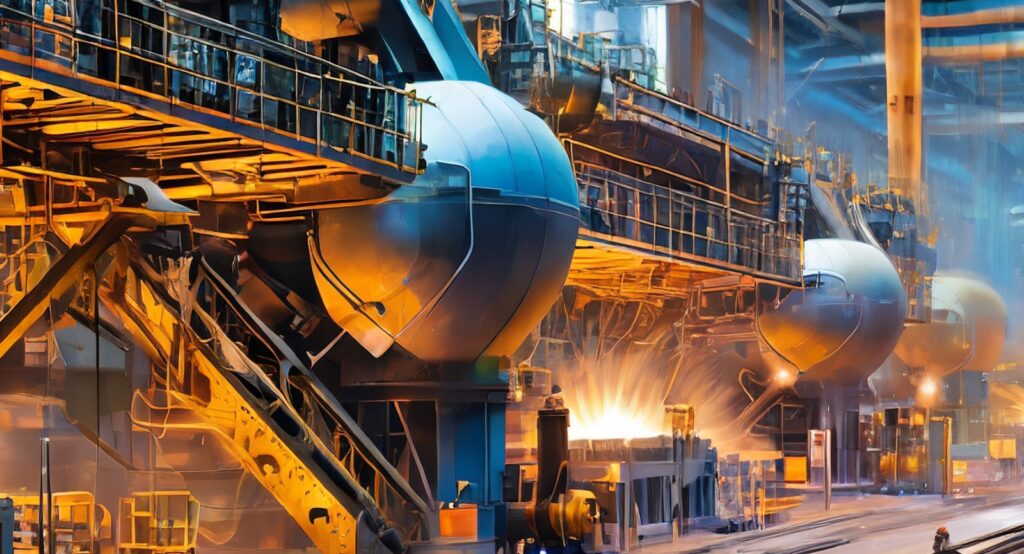
The Imperative of Operational Excellence
Operational excellence is not just a goal but a fundamental requirement in the steel manufacturing industry. It represents the key to enhanced efficiency, reduced resource waste, and superior product quality. Adopting lean methodologies is vital in an environment characterized by stringent environmental regulations and intense global competition. These practices optimize resource use, reduce environmental footprint, and meet the high-quality standards expected by customers. Through operational excellence strategies, steel plants can remain adaptable to market shifts, manage
operational costs effectively, and maintain the highest standards of quality, all while ensuring workplace safety and boosting employee morale.
Success Metrics Aligned with
QCDSM
Applying methodologies like the 20 Keys in steel manufacturing has brought about significant
benefits. We outline how these practical implementations have positively influenced Quality, Cost,
Delivery, Safety, Morale, and Technology (QCDSMT) in the context of steel plants:
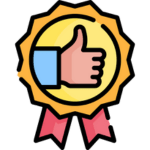
Q-Quality Enhancement
.
- Reduction of production defects by 30-50% in the first year of implementation.
- Achievement of a near-perfect quality output, with quality rates soaring to 99%.
- Significant decrease in customer complaints and product returns.
- Increase in customer satisfaction by 20-40%, as affirmed by customer feedback.
- Increased uptime for machinery and furnaces, achieving over 90% operational availability.
- Reduction of equipment failure and maintenance costs by up to 80%.
- Decrease in inventory levels by around 50%, significantly improving cash flow.
- Energy cost savings in the range of 15-30%, tailored to specific energy-saving measures.
- Reductions in inspection and rework costs by 15-30%.
- Control of process spillage and raw material waste, achieving reductions up to 90%.
- Yield rate enhancements to nearly 99.5%.
- Extension of equipment and machinery lifespan by up to 400%.
- Production costs are reduced by 15-30%, chiefly through waste minimization and process
enhancements.
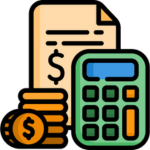
C-Cost Efficiency
.

D - Delivery and Output Optimization
.
- Improvement in production output by up to 85%+.
- Streamlined production schedules ensuring on-time delivery, achieving a 99% Measure of Total
Inventory Free Effective Flow (MOTIFEF). - Enhanced supply chain management, achieving a 99% Delivery on Time in Full Effective Flow
(DOTIFEF). - Reduce and achieve targeted metal melting time.
- Creation of a safer, more vibrant work environment.
- Significant reduction in material spillage and waste, by up to 90%.
- Drastic decrease in search and wait times, by about 90%.
- Reduction in required storage space by 40%.
- Up to a 30% increase in employee morale and engagement.
- Fostering employee involvement in improvement processes, enhancing ownership and
satisfaction. - Encouragement of skill development through cross-training, augmenting job satisfaction.
- Development of a positive, collaborative organizational culture via small group activities and
effective communication.
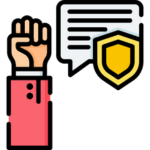
SM - Safety and Morale Advancements
.
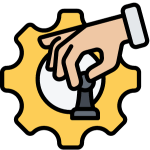
Additional Strategic Advantages for Steel Plants
.
- Enhanced Market Competitiveness: Achieved through cost efficiencies and operational
effectiveness, crucial for steel plants in a competitive market. - Increased Adaptability: Enabling steel plants to navigate market and technological shifts
effectively. - Commitment to Environmental Sustainability: Through focused resource conservation and
eco-friendly practices, aligning with global environmental standards. - Ease of Certification and Audit Compliance: The 20 Keys framework facilitates obtaining
industry certifications and ensures readiness for various audits, demonstrating a high level of
operational integrity. - Long-term Organizational Benefits: Implementation leads to sustained process improvements,
contributing to the long-term resilience and prosperity of the steel plant.
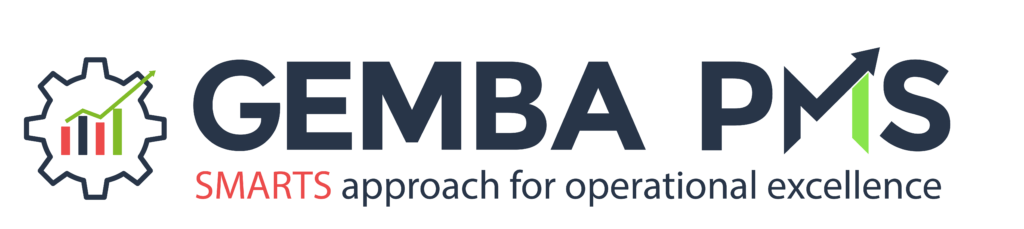
Conclusion
Adopting the 20 Keys framework with Gemba PMS for steel plant managers and top management translates into a strategic partnership that deeply understands the unique challenges and opportunities within the steel industry. Our commitment extends beyond mere implementation; we aim to be your guiding partner towards achieving operational excellence. With our profound industry knowledge and focused approach, we ensure impactful implementation for a notable return on investment. We join you in this journey, leveraging our expertise to transform your steel manufacturing operations into a paradigm of efficiency, quality, and sustainability.