Many organizations embark on the journey of improvement by drawing inspiration from the practices of industry leaders and initiating various projects. However, their efforts often need to improve over time. The critical oversight is their failure to recognize that successful entities adopt a comprehensive strategy for continuous enhancement across all operations. Rather than concentrating on isolated initiatives, these exemplary companies implement a unified, coherent strategy encompassing a broad spectrum of improvement measures. They ensure inclusive participation, making every member of the organization an active participant in this continuous improvement journey. This approach fosters a culture deeply rooted in the pursuit of excellence, encouraging every individual to contribute to ongoing progress.
In essence, achieving sustained success goes beyond the sporadic implementation of improvement tactics; it requires a meticulously planned and all-encompassing approach that engages the entire organization. By doing so, these companies cultivate a robust internal culture and capability for continuous growth and excellence, setting a strong foundation for lasting achievements
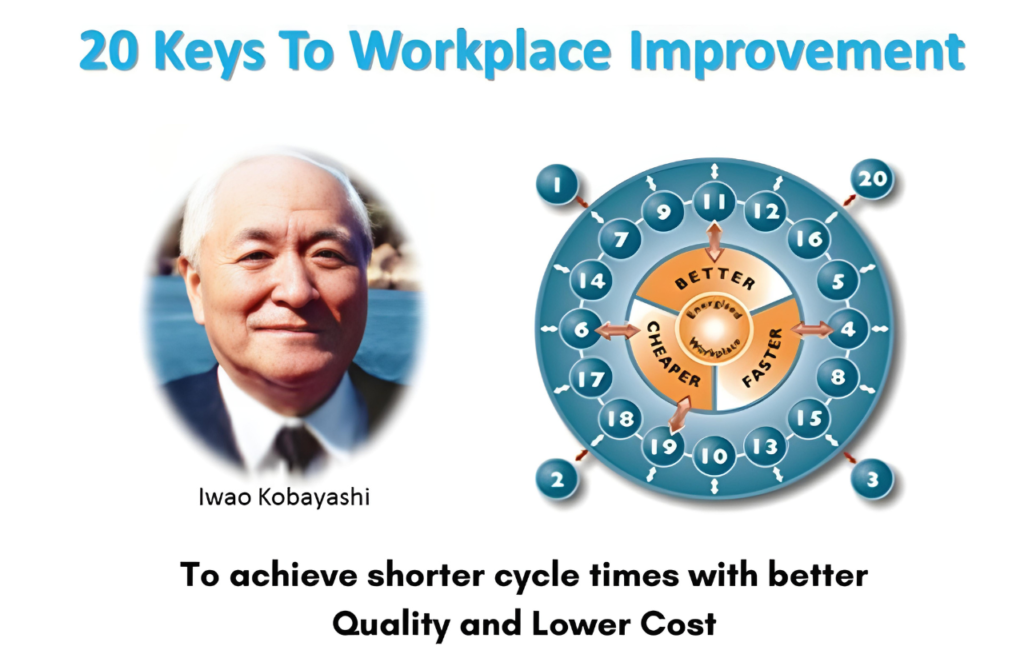
20 keys
The 20 Keys system, a cornerstone in operational excellence, originated in Japan, crafted by Iwao Kobayashi during his tenure at Mitsubishi Heavy Industries. Following his academic pursuits in industrial studies, Kobayashi embarked on a professional journey with the company, where he distinguished himself by pioneering the first mixed-lot automated assembly line in Japan, a feat possibly unparalleled globally at the time. His expertise extended to quick changeover technology, a field in which he worked alongside other eminent Japanese engineers such as Taiicho Ohno and Shigeo Shingo.
20 keys system emerged from Kobayashi’s direct engagement with hands-on learning opportunities, incorporating insights from employees, the shop floor, and cutting-edge production technologies. Kobayashi’s contributions culminated in the publication of “20 Keys to Workplace Improvement,” a book that continues to serve as an indispensable guide for enhancing productivity and operational efficiency.
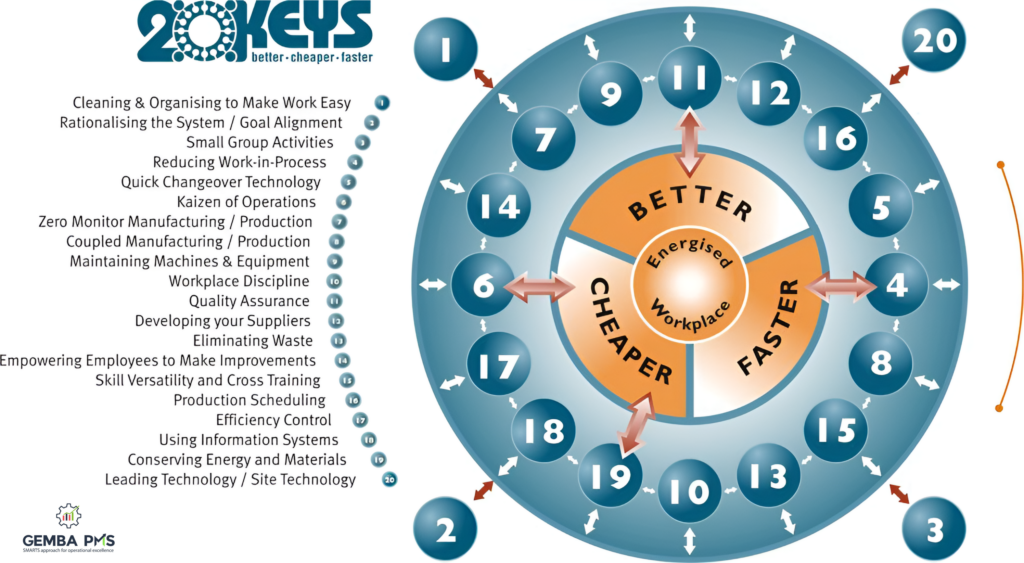
20 keys pms
Aims:
- Top-Notch Operational Performance: Adopt best practices to streamline processes, enhance quality, and reduce waste, elevating efficiency and reliability in delivering products and services.
- Strategic Goals Achievement: Align operational improvements directly with the business’s strategic objectives, ensuring that every effort contributes to overarching targets for growth and market positioning.
- Speed up Learning and Innovation: Foster a culture that values continuous learning and innovation, encouraging collaboration and the rapid implementation of new ideas to stay competitive.
- Eliminate Unnecessary Activities: Streamline operations by identifying and removing inefficiencies, thereby improving product and service quality, speed, and cost-effectiveness, enhancing customer satisfaction.
- Employee Motivation and Engagement: Create an engaging environment where employees are motivated to contribute to the organization’s goals, fostering a sense of ownership and commitment across the workforce.
- Boost Productivity and Profitability: Through these combined efforts, enhance productivity and profitability, securing a strong competitive position in the market over the long term.
Features
- 20 practical and integrated methods form the core of this approach for strengthening organizational delivery systems.
- The primary focus is on enhancing products and services, making them better, faster, and more cost-effective.
- The 20 Keys serve as a roadmap to guide companies toward becoming world-class organizations.
- It helps create a shared vision of the current state (AS-IS) and the desired future state (TO-BE), establishing a common language for improvement.
- Proven methodology ensures sustainable business improvement over time.
- A comprehensive benchmarking system is employed, utilizing visual descriptions (maps) and detailed checklists to showcase improvement levels towards world-class performance.
- Involves everyone in the organization across all levels and functions, fostering a collaborative approach.
- Strengthens initiatives like ISO, HACCP, 6 Sigma, Lean, CRM, GMP, etc., building upon and complementing them for a more holistic improvement strategy.
Benefits
Implementing the 20 Keys approach unifies an organization towards improving quality, lowering costs, speeding up delivery, boosting morale, and ensuring a safe workplace. The notable benefits include:
- Productivity Increase: Up to 200% improvement, showcasing significant efficiency gains.
- Reduction in Mistakes/Defects: Decreases by up to 80%, enhancing product quality.
- Inventory and Work-in-Progress Reduction: Cuts down by as much as 50%, streamlining operations.
- Cost Reduction: Overall savings of around 20%, making operations more financially sustainable.
- Skill Enhancement: Employees’ abilities and competencies significantly improve.
- Morale Boost: Better workplace atmosphere and team spirit.
- Improved Communication: A clearer understanding of business goals and challenges, leading to an improvement in benchmark scores.
The main goal of Key 1 is to make work safer, easier, and more productive by creating tidy and organized workplaces that everyone can take pride in. This results in energized work teams, boosted motivation, and improved productivity for both people and machines.
Key 2 emphasizes having a good organization setup where everyone’s goals are in sync. In this structure, different work groups act like small businesses, each following performance indicators for Quality, Cost, Delivery, Safety, and Morale (QCDSM measures).
Key 3 is all about creating small groups that work together to solve problems. These groups, known as SGAs (small group activities), focus on brainstorming and finding solutions for issues related to quality, cost-effectiveness, delivery, safety, and more. SGAs use a specific methodology along with tools and techniques to address these problems. Additionally, Key 3 encourages everyone to think about improvements, not just those that require a small group, by welcoming suggestions and innovations.
The Key 4 method, along with other strategies, helps a company cut down on work that’s in progress (WIP). This leads to saving space, lowering the need for capital, shortening the time it takes to supply customers, and gaining other advantages related to reducing inventory.
Key 5 offers a way to consistently make changeovers faster. This not only helps in cutting down on the amount of stock in the system but also makes it easier to quickly provide a variety of products to customers.
With Key 6, processes and procedures are analysed, with the objective of improving productivity. Processes and procedures are studied for improvement by means of process flow diagrams like activity flow diagrams and physical flow diagrams, as well as operation improvement sheets.
This key focuses on cutting out unnecessary monitoring to reduce waste. For instance, constantly watching machines or checking for defects isn’t helpful. Instead, the goal is to improve equipment and processes so that problems and defects are prevented from happening. The same idea applies to monitoring people at work – if they are trained well, they should be able to work independently without constant supervision. If issues arise, they can ask for support when needed.
Coupled manufacturing is like a game plan that connects steps in making things. The goal is to make everything run smoothly and quickly, with less stuff sitting around, and good communication between each step. This helps things move along well from start to finish.
This key emphasizes enhancing the performance of machines and equipment. The idea is to engage operators and users in hands-on maintenance, including daily tasks and routine checks, to ensure proper equipment operation. Maintenance artisans and engineers then concentrate on implementing the maintenance plan and employing proactive methods to sustain optimal equipment effectiveness.
This key is all about making the workplace a positive and respectful environment. It’s important to follow the rules, values, and policies of the organization. Everyone should be committed to safety, discipline, and being on time. The key focus is on everyone practicing self-discipline.
The goal of Key 11 is to make sure that we have high-quality work right from the start by focusing on quality in the workplace. The ultimate goal is to have no mistakes or issues by making sure our processes are highly capable. We want to get things right the first time by building quality into the way we do things.
This key focuses on improving relationships with external suppliers of materials and services. The idea is to treat suppliers as partners in the value chain. It introduces a structured approach for handling and enhancing supplier relationships, using a supplier development strategy, supplier service agreements, and evaluating supplier performance. These principles are also applied to internal suppliers, such as upstream processes within the organization.
Key 13 is all about cutting out unnecessary things at work. Waste means anything that doesn’t help or add value. This key is about not wasting time, especially how people use their time at work. The goal is to spend more time doing things that really matter and make a difference.
Team empowerment is characterized by well-informed, multi-skilled team members who take initiative, can investigate problems, are empowered to make decisions, and implement improvements suggested.
Skill versatility and cross-training are all about continuously learning and growing in the workplace. It’s a part of the business plan to help people gain more skills and become really good at what they do. The goal is not just to make individuals better, but also to have teams that can do many different things well. This goes for both the teams that make the products and the ones that support them. It’s all about being flexible and having lots of skills across all teams.
Key 16 focuses on making sure that production and work schedules are consistently met, and deliveries are made on time to customers. To achieve this, various scheduling principles are applied, such as planning backward, using finite scheduling, measuring schedule achievements at specific points, load leveling, tracking work progress, and employing visual management techniques.
Efficiency control involves setting realistic and motivating goals for tasks and processes, with input from production and support teams. Teams actively participate in establishing targets, and then measure their actual performance against these goals to monitor and improve their work.
In Key 18, the focus is on making sure that the computer systems we use at work match up with what the company is trying to achieve. This means they should work well together and be a helpful tool for everyone, not just a few people. Everyone should know how to use the systems they need for their job, both for everyday tasks and to make things better over time.
Key 19 is all about getting everyone in the company to know how they can save energy and materials in their jobs. Even small efforts add up and help the company save money. It’s not just about knowing, but also always finding new ways to save energy and materials by using the right technologies. This helps the company be more cost-effective.
Leading technology refers to the tools and equipment a company uses to create its products or services. Site technology, on the other hand, is all about the skills and knowledge the company has gained over time. In Key 20, the crucial factor is how quickly the company adopts and adapts to new technologies.
Exploring the 20 Keys system reveals its potential to revolutionize organizational operations. Gemba PMS, the licensed implementer in East Africa (Kenya, Tanzania, Uganda, Ethiopia), brings a profound understanding of this methodology. Our approach surpasses mere training, aiming for a deep, sustainable integration of the 20 Keys system at every organizational level.
Our strategy at Gemba PMS is customized and comprehensive. We don’t just implement; we immerse ourselves in your organization to cultivate a culture of continuous improvement. With Gemba PMS, the 20 Keys system evolves from a method to a driving force for efficiency, innovation, and excellence.
Partnering with Gemba PMS guarantees a transformation tailored to your needs, ensuring a lasting impact. Let us guide your journey to operational excellence. Contact Gemba PMS to start transforming your organization with the 20 Keys system today.
20 KEYS
GLOBAL
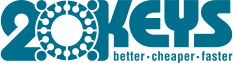