Lean Management methodology
Lean Management -A journey of waste reduction.
Lean is a management approach to maximizing productivity while minimizing wasteful activities from the overall process. Lean thinking defines waste as anything that doesn’t add value to a customer or business. Lean ideology is based on and driven by specific continual improvement tools & techniques that have influenced overall processes worldwide (CI tool & techniques glossary). With time, Lean thinking is becoming an organizational culture that can go beyond waste reduction.
5 steps of Lean Management

Purpose of lean management.
- Improve quality
- Reduce operating costs
- Improve speed of delivery
- Improve Safety & Moral
TIM WOODS Is an acronym that represents the 8 forms of Waste found in Processes that should be reduced or eliminated.

In an era where efficiency defines success, Lean management is a key strategy for businesses aiming to streamline operations and cut waste. Central to this approach is TIMWOODS, a mnemonic that highlights eight areas ripe for improvement: Transportation, Inventory, Motion, Waiting, Overproduction, Overprocessing, Defects, and Skills. This simple yet powerful tool guides companies in identifying and eliminating inefficiencies, paving the way for enhanced productivity and a leaner operation.
Embracing TIMWOODS goes beyond just trimming down waste; it’s about cultivating a culture of continuous improvement and innovation. By scrutinizing processes through the TIMWOODS lens, organizations unlock the potential to save costs and engage and empower their workforce. This journey towards operational excellence encourages a collaborative environment where every employee drives the company forward, fostering a more agile, resilient, and competitive business.
Let’s break down and understand these wastes to make our work processes better.
T – Transport: Moving materials more than necessary increases costs and risks.
In simple terms, moving a product around without a good reason is a waste of time and effort. It also raises the chances of the product getting damaged.
In an office setting, unnecessary movement of things happens a lot. This includes big things being shipped globally and small things being shuffled around in offices just to get to something at the back of a cupboard.
In our homes, think about how we move around in the kitchen to grab a mug and boil water. Maybe you’ve set up your coffee supplies close together, like having the coffee next to the kettle or the cups right by the machine. It’s all about finding the best way to save time and effort. And then there’s the daily routine of getting kids to school or their after-school activities. For parents, it’s always a juggling act, trying to make the most of time and minimize the distance between tasks.
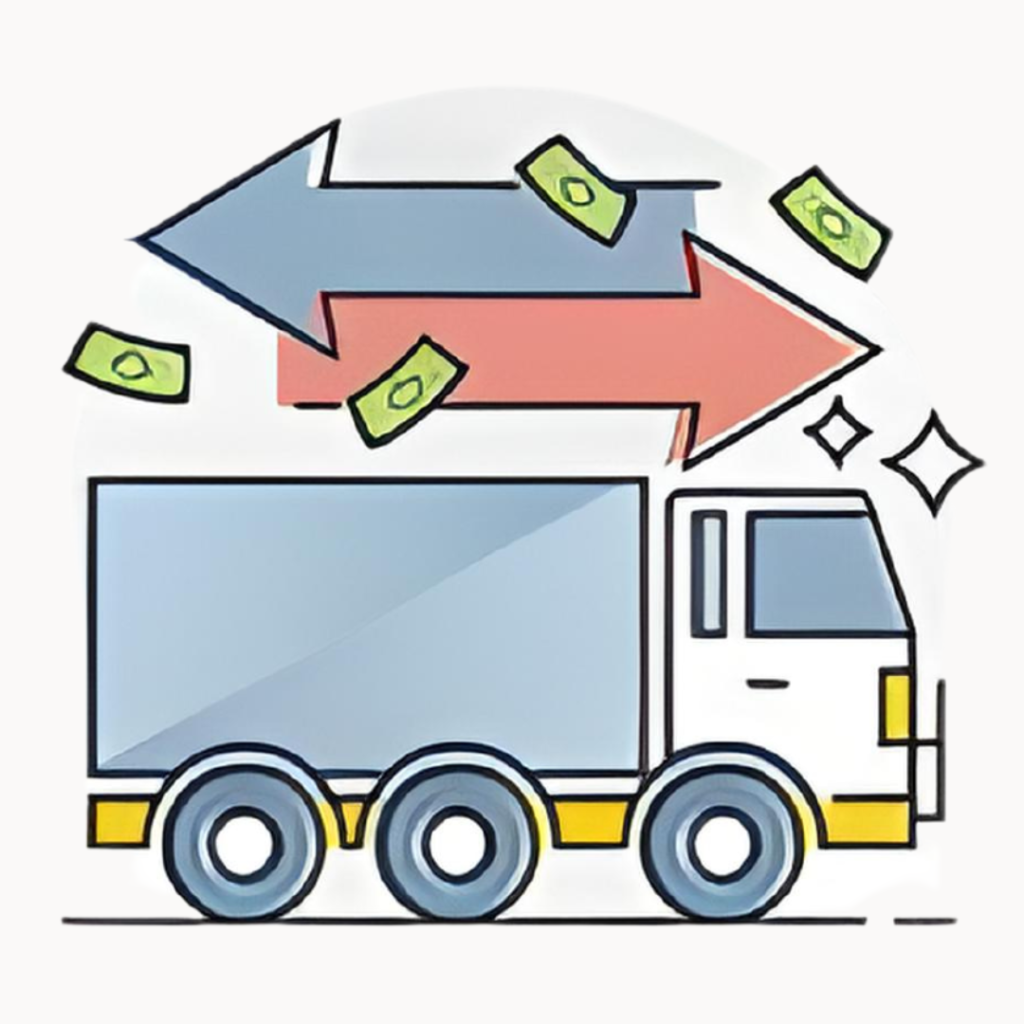
Timwoods Tr
Transportation is a big problem in getting things done efficiently, as pointed out by Taiichi Ohno from Toyota. When things are moved around, they don’t improve or add value for the customer. This can be easily seen when stuff is moved between factories, workstations, or departments.
Not all transportation is bad, though. For example, companies like Amazon need transportation to deliver goods. But what’s really wasteful is unnecessary transportation. Amazon and other delivery companies struggle to deliver to customers on the first try, which is a waste for both the customer and the company. That’s why they’re trying out new methods like using drones or delivering directly to your car’s trunk. They want to make sure they get it right the first time.
So, whether it’s in your office, business, or home, look out for unnecessary transportation. Cutting down on it is a great way to save time, effort, and reduce waste, which directly affects both your internal and external costs. The goal is to eliminate as much unnecessary transportation as possible or find ways to make it valuable if we have to do it.
I – Inventory: Holding more stock than required ties up cash and space.
Definition: Unused materials equal wasted money. This can be raw materials (0% complete), work-in-process (50% complete), or finished goods (100% complete).
In the office: Inventory is anything you have in excess, like spare parts, papers on your desk, or an overflowing inbox with thousands of emails. Inventory in businesses, whether finished or unfinished goods, costs money due to purchase, storage, depreciation, and expiry costs, both digital and physical.

Timwoods d
In the home: Your kitchen cupboard, garage, storage room, or that spare room you rarely use are examples of inventory. Buying in bulk or getting 2-for-1 offers creates inventory at home, tying up money in products you won’t use immediately. Decluttering methods like the KonMari method can help manage inventory at home.
Inventory is a pure cost, whether in business or at home. It requires money, time, physical effort, labor, and invested capital that could be used elsewhere.
One goal of Lean is to minimize inventory, promoting a constant state of flow and efficiency. So, take a look around your spaces, identify inventory, and realize how much money and resources are tied up unnecessarily. Many companies encourage us to buy more than we need, contributing to the inventory issue.
M – Motion: Excessive employee movement wastes time and energy.
In simple terms, “motion” refers to unnecessary movement of people or machines that doesn’t add value to a process. For example, in a business setting, constantly walking to the photocopier or between workstations without accomplishing anything of value is considered motion.
At home, think about the kitchen – moving back and forth between cupboards, the stove, the dishwasher, and the fridge can be a lot of unnecessary motion. Imagine drawing a line on the floor every time you move around while cooking – it might look like a tangled mess!
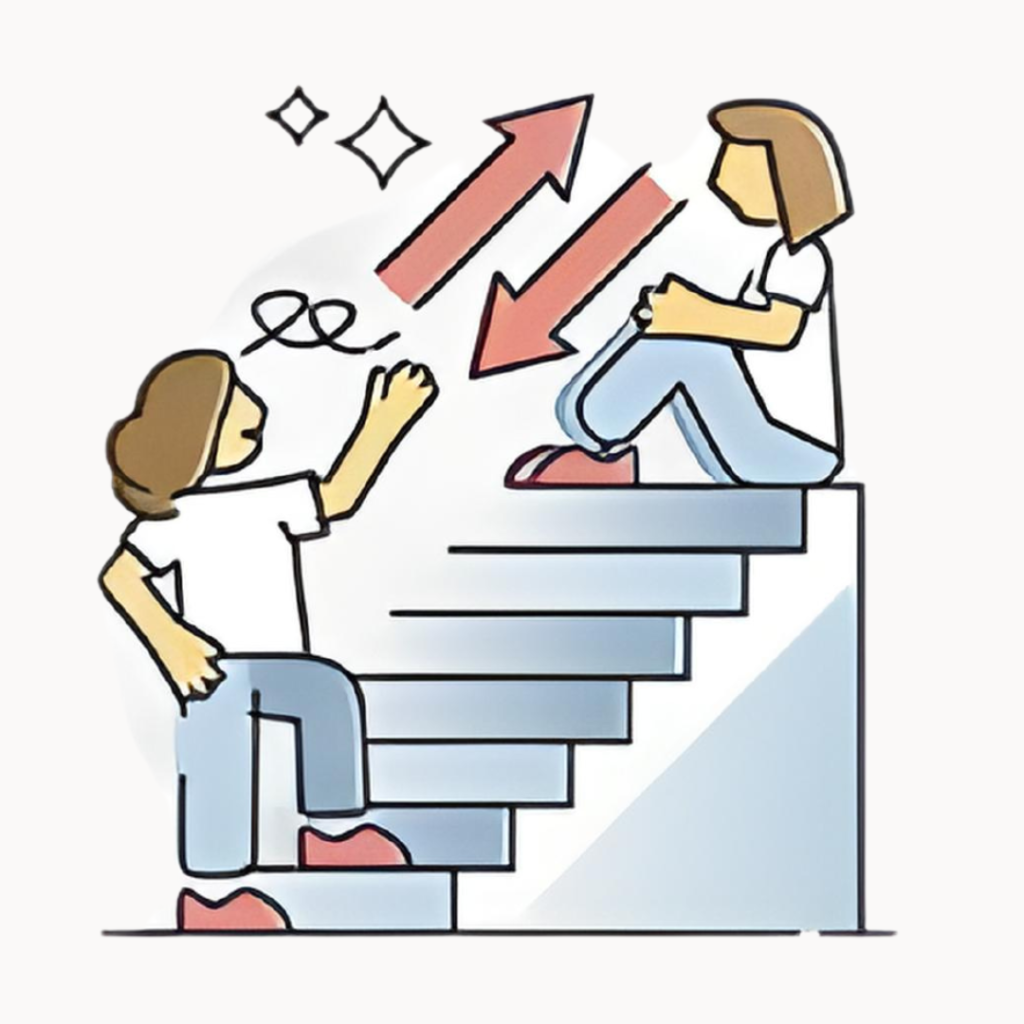
Timwoods M
This unnecessary motion disrupts the smooth flow of tasks and can be a problem in both business and home settings. In business, waiting for people to travel and meet in the same location can disrupt the flow of work, especially when teams are spread out geographically. Web conferencing can help reduce this kind of motion.
Printers and photocopiers can also create unnecessary motion in an office. When these machines are centralized, it can lead to queues, waiting times, and even forgotten printouts. While printers are necessary, finding ways to manage the flow around them or reducing the need for printing altogether can help improve efficiency.
W – Waiting: Idle time reduces overall efficiency and throughput.
Definition: Waiting time is when a product is just sitting there, not being transported or processed. It’s the time people spend waiting for a product to arrive, and it’s considered the biggest and most frustrating waste.
In the office: Waiting is like a virus when there’s a lot of motion. It’s the most expensive among the 7 Wastes because it not only delays things but also wastes a lot of team time. Think about how many follow-up emails you send, asking if someone has had a chance to do something. Recently, it was known that someone waiting for 4 weeks just to get a signature for a project. Waiting can happen for various reasons, like waiting for a delivery, IT to fix your computer, or an outsourcer to provide a software update. It could also be waiting for approval to do something you already know needs to be done.
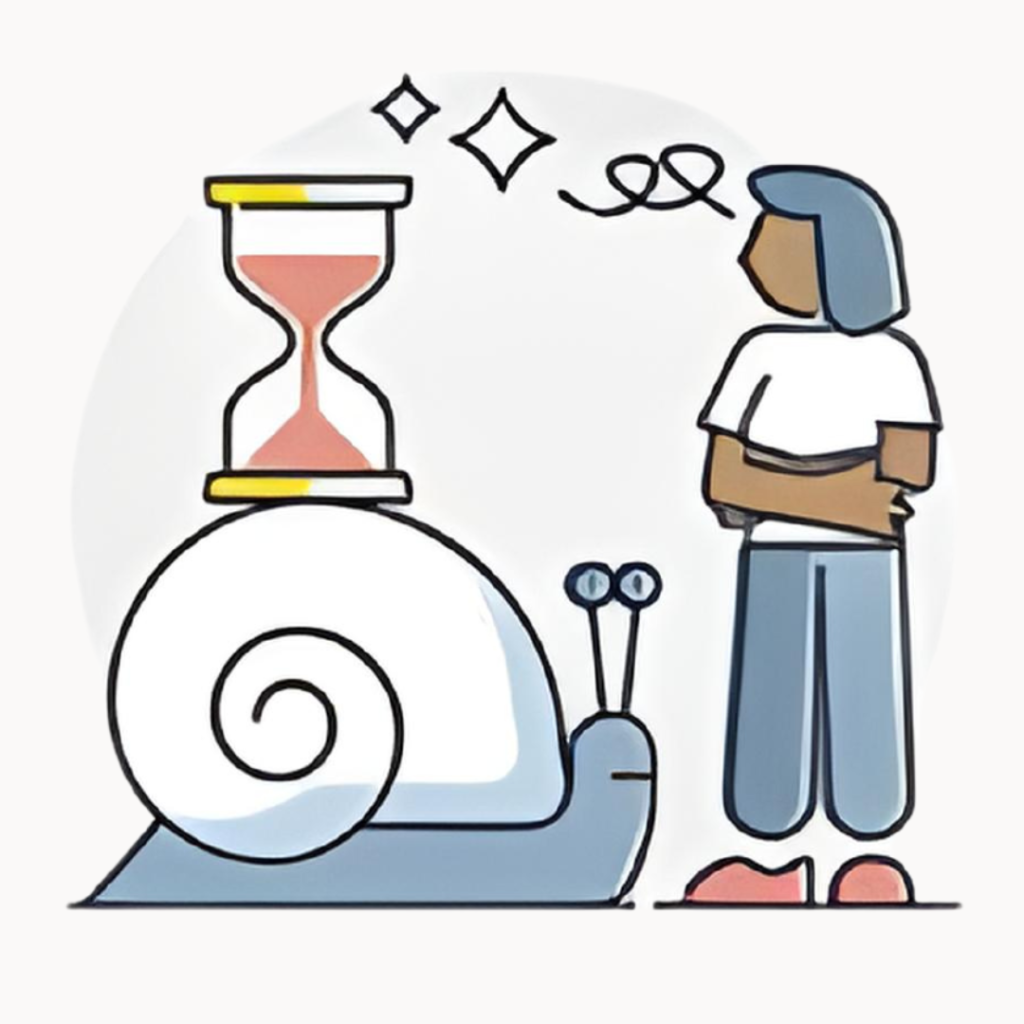
Timwoods T
Let’s not forget the time wasted waiting for people to join meetings or conference calls on time. Imagine 10 people waiting for 15 minutes for the lead person to join – that’s 150 minutes of productive time lost and a considerable amount of salary down the drain. Waiting losses are something no one really likes.
In the home: Waiting is just as bad in our personal lives. Have you ever waited for someone to show up for dinner, and they’re an hour late? Or waiting at home for a delivery? How about being stuck in traffic on the way to work? And then there’s the doctor’s waiting room – another place filled with waiting and lost time.
In our personal lives, we can try to make waiting time valuable by finding things to do during the gaps, but waiting is still waiting. It happens when two independent processes are not synchronized. Whether it’s suppliers delivering late or customers arriving early, waiting disrupts the flow and destroys value.
Waiting is one of the biggest and most frustrating wastes among the seven. The costs – in terms of dollars, time, and frustration – are huge and often underestimated by senior management. Our goal should be to identify where “waiting is hiding” and find ways to synchronize processes to minimize it as much as possible.
O – Over-processing: Adding unnecessary steps or materials inflates costs.
Definition: Over-processing means doing more to a product or service than necessary, going beyond what the customer is actually paying for.
In the office: Over-processing is a common issue where we often go above and beyond, thinking we’re being helpful to the customer. However, this can cost the company time and money, as we’re delivering more than the customer is paying for. Additionally, consistently over-delivering can set unrealistic expectations. This problem exists not only with external customers but also among internal teams. For example, producing a detailed sales report when the internal customer only needed one figure is a clear case of over-processing.
In Lean Six Sigma, the goal is often to achieve six sigma quality, but the question is whether this level of perfection is always necessary. The costs of going from four-sigma to six-sigma can be substantial, and in some industries, a lower level of quality may be sufficient.

Timwoods OE
In some industries, clients are charged based on hours worked, leading to a common issue called “over-servicing.” This happens when the agreed-upon hours are exceeded, resulting in higher costs without clear benefits to the client.
In the home: Identifying over-processing in personal life can be tricky, but one example is the excessive management of digital photographs. Storing them on various devices, transferring to backup drives, and uploading to virtual drives can be unnecessary. Another example might be over-maintaining a car by taking it to the garage too often.
Identifying over-processing is challenging, especially when customer requirements are not clearly defined. The key is to start by clearly understanding the customer’s needs and what they truly value. This applies to both external and internal customers.
O – Overproduction: Making more than needed leads to excess inventory and waste.
In the workplace, over-production happens when we make more things than necessary. It’s a common issue in businesses where we fill our shelves with extra items, print more than we need, or produce more than is required, thinking we’re doing the right thing. The problem with over-production is that it leads to excess inventory, making the process inefficient.
This becomes a bigger problem as customer needs change quickly. Unlike 20 years ago, when we could produce a large quantity and sell over a long period, today’s fast-paced world makes over-production risky. If customer demands shift, the excess items become obsolete, needing disposal. Over-production not only makes us look busy but also leads to a buildup of unused items.

Timwoods OP
In our homes, we also deal with over-production. When cooking, we tend to make extra just in case. Similarly, when shopping, we buy more than needed, often falling for discounts that only increase cupboard clutter.
One of the key principles of Lean thinking is to create processes that flow smoothly. Over-production disrupts this flow by creating unnecessary inventory, hiding underlying issues. Many consider over-production the worst waste of all.
Industries, like the automotive sector, have moved away from bulk processing to just-in-time delivery. Supermarkets and Amazon manage their inventory efficiently to provide customers with what they need, when they need it, minimizing excess stock.
The fear of missing out or running out of something drives over-production in both work and daily life decisions. People tend to stay busy or appear busy, leading to the habit of doing more than necessary. Incentives like bonuses based on the quantity of units made or transactions processed contribute to this problem. At the end of the year, businesses often engage in unnecessary spending or production to use up their yearly budget.
D – Defects: Errors require rework and harm customer satisfaction.
The last of the seven wastes is something we can all relate to – Defects. Defects happen when something in a process isn’t done correctly and needs to be redone or fixed.
In the office, we deal with defects every day, from filling out a form wrong to a key product not working and needing rework. Organizations often have customer service centers to handle complaints and issues. Defects cost businesses a lot of money and effort to fix.
There’s a rule called the 1:10:100 rule, which means fixing an error immediately costs x dollars. If it’s caught later, it’s x10, and if even later, it’s x100. Think about vehicle recalls – a major defect can lead to recalling thousands of vehicles. Even things like scrap paper or materials are considered defects. It’s important to have an open culture where people can admit mistakes without fear of blame.

Timwoods 1
Similar issues arise at home. Poor quality in home improvements or dealing with warranty repairs can be frustrating and time-consuming due to defects.
In conclusion, defects not only cost money and resources for businesses but also lead to customer dissatisfaction, pushing them to seek alternatives.
S – Skills Underutilization: Not fully leveraging employees’ abilities and creativity limits innovation and growth potential.
The eighth waste, often overlooked, involves not making the most of people’s skills, talents, and interests. In today’s highly competitive business environment, utilizing the untapped potential of employees can be a game-changer for long-term success. Unfortunately, many individuals find themselves in roles that don’t align with their strengths, leading to boredom and a search for new opportunities on platforms like LinkedIn.
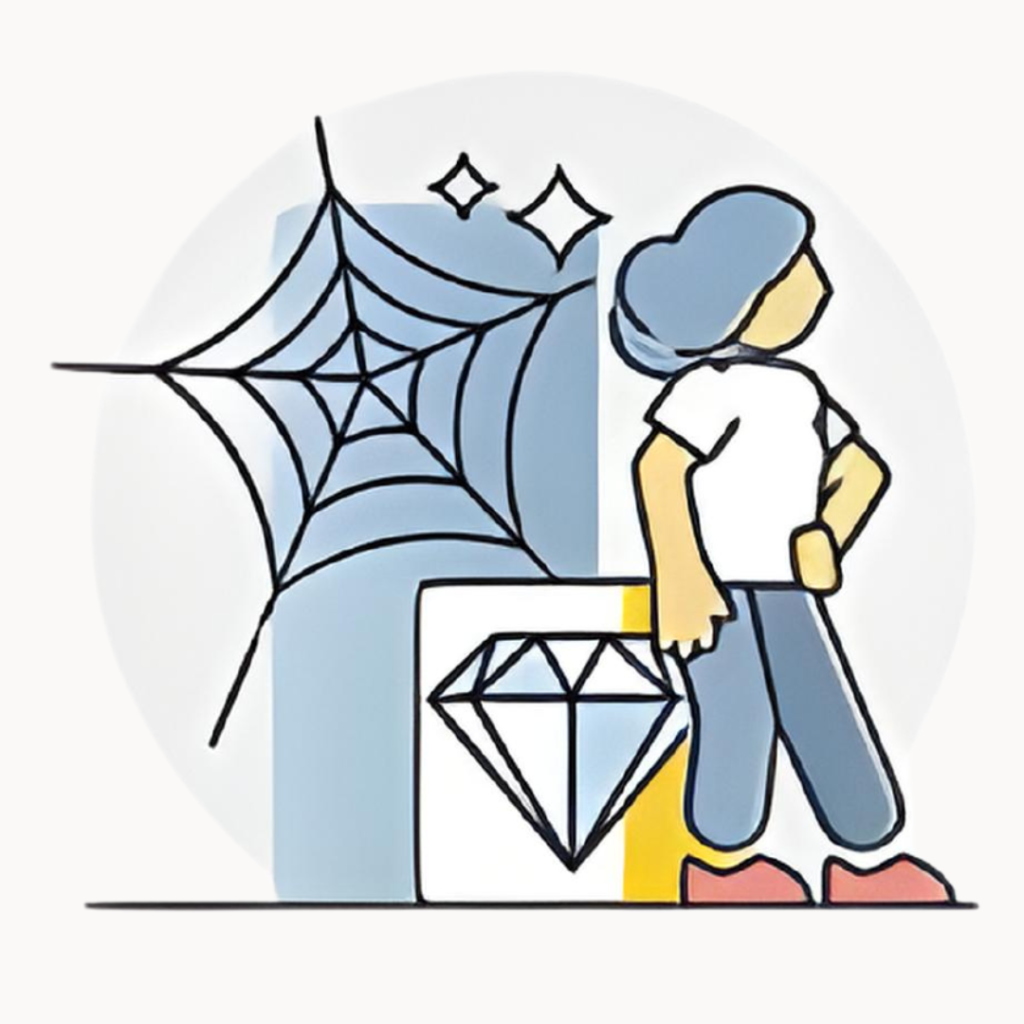
Timwoods US
Despite the common saying that “people are our greatest asset,” this waste persists, and it’s actually getting worse over time, rather than improving.
In Conclusion, time is a precious commodity, and cutting down inefficiencies is crucial for business success. The TIMWOODS approach, focusing on eliminating key wastes like unnecessary movements, excess inventory, and idle time, is transformative. Lean Thinking empowers organizations to conserve resources and elevate efficiency.
At Gemba PMS, we specialize in Lean Management (and 20 keys), including adeptly applying the TIMWOODS methodology. We guide businesses through the complexities of reducing waste and enhancing processes. It’s not merely about process improvement; we stress the importance of effectively leveraging team skills. Partnering with us allows companies to efficiently address the eight wastes, adopting Lean principles to boost productivity and navigate towards a more prosperous future. With our expertise, embracing Lean with Gemba PMS transforms efficiency goals into achievable outcomes, ensuring sustainable growth and success.
Lean Six Sigma Methodology
Lean Six Sigma – Statical management approach for problem-solving.
Six Sigma (6σ) strategies seek to improve manufacturing quality by identifying and removing the causes of defects and minimizing variability in manufacturing and business processes. This is done by using empirical and statistical quality management methods and hiring people who serve as Six Sigma experts. Each Six Sigma project follows a defined methodology and has specific value targets, such as reducing process variances and errors, streamlining operations, or increasing customer satisfaction.
Five steps of Lean Six Sigma.

Purpose of Lean Six sigma.
- Find and eliminate variance.
- Improve productivity.
- Rescue the cost of operations.
- Improve customer satisfaction.